Unique requirements of uninterruptible power supplies for naval applications (free whitepaper)
This whitepaper is brought to you by Enercon Technologies Ltd.
A true Naval qualified – MIL-STD-1399 and MIL-DTL-901 - Uninterruptible Power Supply (UPS) must meet stringent requirements, consistent with a military quality solution. This white paper reviews a set of core qualifications to evaluate when sourcing a military UPS.
Introduction
All of Enercon Technologies Ltd’s Uninterruptible Power Supplies (UPS) are designed and built specifically for Navy Shipboard (Surface and Submarines) applications.
A UPS intended for Navy ships must meet stringent requirements that are specific to Navy applications and are not required in almost any other application. It is almost impossible to modify the design of a UPS that was not originally designed for Shipboard application, such that it will be able not only to reliably operate from Ship‐board power and tolerate the ship environments. But also, to ensure that it will not compromise the ships safety and combat readiness (for example, by generating structural born acoustical noise in a Submarine) or interfere with the operation of special equipment (for example, by generating low frequency power‐line harmonics that interfere with the operation of Anti‐submarine Warfare Equipment).
ABOVE: The Enercon Technologies Ltd. M359-1 2.2KVA, 115V, 60Hz UPS
Some of the features that affect the quality and reliability of a Naval UPSs are very similar to those required for similar high-quality equipment intended for other applications. High quality Workmanship and Soldering (per IPC J‐STD‐001 and IPC‐A-610), Conformal Coating on electronic assembly (per MIL‐I‐46058C and IPC‐CC‐830), the segregation of humid and dust‐laden cooling air from circuit boards and power semiconductors, corrosion preventive measures and other best‐practices are important for any high-quality electronic equipment.
Several of the special requirements from a UPS intended for a Navy Shipboard application, that are typically not required from a standard high‐quality UPS designed for other applications are delineated on the following pages.
This requirement, unique to MIL‐STD‐1399‐300B, is difficult to meet and requires a special design of the input power stage of the UPS
— Enercon Technologies Ltd.
Input Power
The characteristics of Shipboard Power (Typically: Type I, 115 or 440VAC, 60Hz) that the UPS should be able to reliably tolerate and operate from, are specified in Paragraph 5.1 of MIL‐STD-1399‐300B. However, compatibility only with the characteristics specified in Paragraph 5.1 is not sufficient to ensure compatibility with shipboard power, far from it.
Paragraph 5.2 of MIL-STD‐1399‐300B specifies the mandatory requirements from User Equipment (that the UPS is typically the front‐end of).
For example: Para. 5.2.9 (Input Current Wave Form) requires that the input current that a User Equipment rated at 1KVA or higher, powered by the ship must be a low-distortions sine-wave with none of the 60Hz harmonics exceeding 3% of the fundamental. This requirement, unique to MIL‐STD‐1399‐300B, is difficult to meet and requires a special design of the input power stage of the UPS. In contrast with common (but erroneous) belief, a high-power factor does not ensure low distortions.
As shown below, a load with harmonic current distortions as high as 14%, can still have a Power Factor higher than 0.99.
Environment Conditions
The Naval shipboard environment is characterized by low‐level vibrations (specified by MIL‐STD‐167‐1A) caused by the ship’s propulsion system and by the interaction between the hull and sea. Due to the low frequency of the vibration, the ability of shock absorbers, or similar mechanical isolators, to attenuate the vibration is limited and the equipment (UPS) must be able to reliably tolerate the specified vibration.
Shocks and Vibration
An even more stringent requirement is the High Impact Shock specified by MIL-DTL-901 (also known as the “Hammer” or “Barge” tests). These tests verify the ability of the equipment to remain safe and provides performances (if applicable) when the ship is hit by a high impact weapon (such as the detonation of a near-ship depth-charge). If a UPS is not specifically designed for these high impact shocks, the very high peak level and very low resonance frequency of the shock, not only will damage it, but may result in safety hazard if parts of it disintegrate and become lose projectiles.
A typical failure mode of UPSs that are not designed for this environment is a failure of the internal batteries during vibration and/or High Impact Shock test. In a typical commercial or industrial UPS, the internal batteries are secured in place only by straps or other similar fast-release mounting provisions. Typically, this means that it does not hold the battery cells securely enough and during low-frequency vibration the cells “bounce” in place and may suffer permanent damage. When exposed to high impact shock (especially if it immediately follows the vibration test that has loosened the straps) the heavy cells may get completely loose and “fly away”. Using mechanical isolators between the rack that hosts the UPS to the ship’s hull, can reduce the shocks peak level, but typically introduce mechanical resonance at low frequency that may increase the vibration level that the equipment will be exposed to.
Electro Magnetic Environment
The EMC requirements that are applicable to UPSs for Naval Shipboard application are specified in MIL‐STD‐461 and MIL‐STD‐1399 Section 070. Most of the EMC requirements in MIL‐STD‐461 are similar to those for other applications. There are a few requirements however, that are unique to Naval application.
Input to Chassis Capacitance: MIL‐STD‐461 (Para 4.2.2) puts a limit on the maximum capacitance between the AC power lines and chassis that is allowed for Naval application (similar limit appears in MIL-STD‐1399‐300B).This requirement is unique to Naval Ships (both surface and submarines) and put a severe limitation on the size and effectively of the line‐to-ground EMI filters that may be used on the AC input lines. In order to mitigate this problem, the electrical and physical layout of the power switching circuits of the UPS must be carefully designed such that the generation of a common mode electromagnetic noise by stray capacitance to chassis is minimized.
Low Frequency Conducted Emission (CE101): This requirement puts a limit on the low frequency conducted emission (CE101) that the UPS is allowed to generate on the AC Input Power lines (a similar, but not identical to the Input Current Waveform requirement of MIL-STD-1399-300B). Attempting to “fix” a UPS, that was not designed for compliance with this requirement, by adding more filters on its input, will almost always fail. CE101 starts at frequencies so low, that passive filtering become impractical (due to the required physical size).
Low Frequency Radiated Emission (RE101): This requirement puts a limit on the radiated near-field emission of the UPS at low frequencies. Complying with RE101 requires a careful magnetic design of the power circuits and especially of the magnetic devices such as transformers and inductors. In particular, high power isolation transformers must have a magnetic shield around them made of magnetic (ferrous) material, (aluminum and copper that provide very effective shielding at higher frequencies, do almost nothing at the low frequencies specified by RE101).
Tolerance for Strong DC Magnetic Field: MIL-STD-1399 Section 070 requires that the equipment will not be affected by the strong DC magnetic field generated by the ships degaussing equipment (that manipulates the ship’s magnetic signature). DC magnetic field is not attenuated by the aluminum enclosure of a typical rack and may severally effect transformers, inductors, current sensors and other magnetic devices. If not designed for, the strong DC magnetic field specified by MIL-STD-1399 (Section 70) may drive the transformers and inductors that are used in the power circuits into saturation, resulting in a permanent catastrophic failure of the UPS.
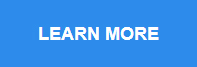
More from German Defence Industry Special Report
-
German Army to upgrade combat vehicle sims
Saab is to carry out a mid-life upgrade programme of the German Army’s AGDUS combat vehicle simulators, the company announced on 4 December. The $18.9 …
-
Power conversion: the value of customisation (free whitepaper)
Are the benefits of a power conversion solution which truly fulfills the application requirements found in a tailored solution? This white paper reviews the challenges …
-
Saab to operate German Army’s GÜZ
Saab will operate the German Army’s Combat Training Centre, Gefechtsübungszentrum Heer (GÜZ) between 2020 and 2026 under a new contract announced on 2 December. The …
-
Rheinmetall showcases indirect fire capabilities
Rheinmetall has taken part in a demonstration in South Africa to showcase its indirect fire capabilities, the company announced on 27 November. The test fire …
-
Important factors in vehicle power distribution (free whitepaper)
The purpose of this article is to define the importance of flexibility and customisation in the type of PDU selected for military vehicle and aircraft …
-
Germany's latest industry developments (video)
Watch a summary of the latest developments in the German Defence Industry. Land On land KMW has begun deliveries to Denmark and Germany of the …