The integration issue: how is Avon Protection overcoming challenges in CBRN protective equipment?
Above: Avon Protection’s EXOSKIN-S1 suit is designed to integrate seamlessly with its EXOSKIN-G1 gloves, EXOSKIN-B1 boots, and widely-deployed protective respirators. (Source: Avon Protection)
This article is brought to you by Avon Protection
While the fielding of advanced personal respirators is widespread across NATO nations, many are finding that the purchase of protective CBRN suits, boots, gloves and hoods is long overdue, with much of the currently fielded gear proving bulky, uncomfortable and restrictive for those that rely on them when operating in CBRN threat environments.
However, as procurement programmes target newer, more capable protective garments, the challenges of bringing together systems developed by different companies into an integrated ensemble are proving significant.
“What we are seeing is that the word ‘interface’ is arising frequently in procurement documents, reflecting the challenges being faced by efforts to ensure all the different parts of a CBRN protective system work together effectively,” Justin Hine, Product and Strategy Director at Avon Protection said. “And this is really key, because you can have the most technologically advanced mask, hood, suit, boots and gloves, but if the points where they meet each other are weak, the whole system risks being a protective failure.”
The fact is, that when protective gear is designed, manufactured and procured in a silo the issue of integration becomes the responsibility of the end user rather than being given due consideration and weight during the planning and design phases of a programme. This means that despite the rigorous testing that individual systems undergo throughout their development, the collective protective ensemble may offer less than optimal protection levels, despite the manufacturers of each independent piece of kit doing their job to the letter.
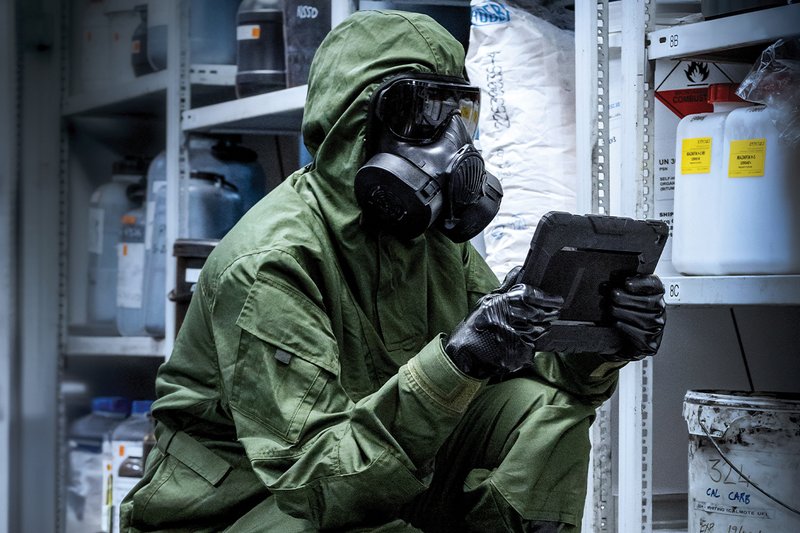
Above:The EXOSKIN-S1 suit is engineered with a cotton poly outer layer and activated carbon inner lining, with an integrated hood with a double elasticated aperture for a secure seal around the wearer’s respirator. (Source: Avon Protection)
“In reality the issue is a bit chicken-and-egg. Military forces and first responders procure equipment individually from different manufacturers because that is how it is developed, with each company operating in isolation,” Hine said. “And to an extent that is understandable from an IP protection perspective. But at the same time, it’s in the manufacturers’ best interest to do so, because when two individually developed pieces of kit don’t work together optimally in the field, manufacturers can point the finger at each other for the failure.”
What is needed is greater cooperation at the industry level, and improved emphasis on acquiring protective kit as an integrated ensemble.
“If we accept that most NATO nations are already fielding advanced respirator systems, the most effective method of building an integrated ensemble is to start with that system and have a single manufacturer take full responsibility for the design and manufacture for the rest of the protective equipment,” Hine said. “By leading with the integration design principle, it puts the onus on the manufacturer to make sure all components work together in the field when the situation gets serious. It also avoids programmes needing to encompass specific interface components, because the interface is part of the design to begin with, which also reduces procurement costs and project delays.”
This is where Avon Protection is positioning itself with a series of developments over the last 24 months. In mid-2022 the company launched its first foray into protective garments with the EXOSKIN-B1 High Traction CBRN Boots and EXOSKIN-G1 Tactile CBRN Gloves. By February 2024, its first offering for the protective suit market was launched with the introduction of the EXOSKIN-S1 CBRN protective suit. Beyond the highest protection levels, ultimate comfort and low burden characteristics, what all systems have in common is an integration-led design ethos.
“With our EXOSKIN series we are approaching the CBRN protection market in a novel way: users can acquire their life-protecting ensemble equipment from a single supplier who is accountable for the entire CBRN equipment ecosystem,” Hine said. “We have engineered all aspects of the equipment to ensure that the most common weak points – at the wrist, ankle, respirator mask/hood interface – are minimised, to deliver superior protection levels for users who would otherwise need to rely on disparate products.
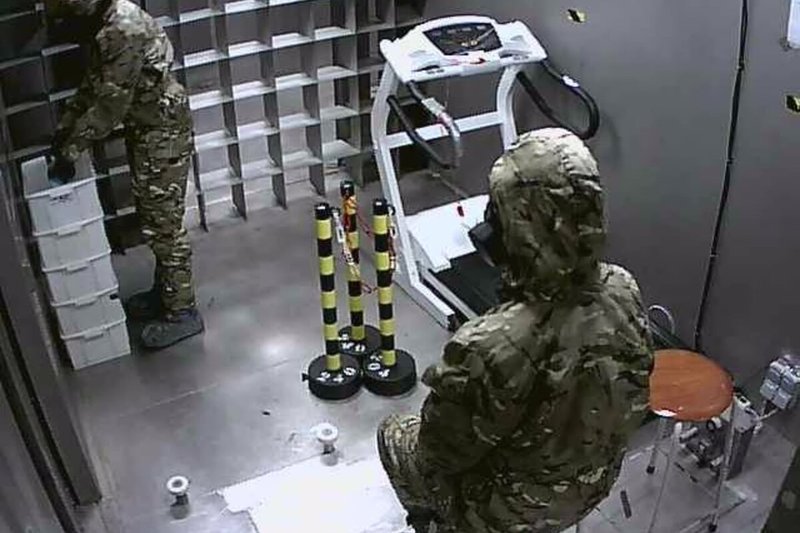
Above: The EXOSKIN-S1 suit completed successful MIST testing to achieve the AEP-38 standard as part of a full-body ensemble with Avon Protection boots, gloves and respirators. (Source: Avon Protection)
“This goal has been backed up by our successful Man in Simulant Testing [MIST] for the EXOSKIN-S1 to achieve the AEP-38 standard. We conducted the testing with the full EXOSKIN suit, boots and gloves ensemble with the Avon Protection FM50 respirator, and successfully achieved the standard – something we believe to be an industry first.”
What this means in practice is that each aspect of carrying, donning, wearing, doffing and decontaminating each garment has been designed with the entire CBRN ensemble in mind, including current in-service respiratory protection masks. In the case of one of the largest user groups – the US military - this is the M50 Joint Services General Purpose Mask and M53 multi-role Respiratory Protective Equipment System, both produced by Avon Protection. Between them, these products protect all personnel in the US military, and have done since 2008, giving the company a significant advantage when it comes to understanding how to also make new protective garment ensembles integrate seamlessly with in-service equipment from a design standpoint.
In fact, at the Defense Threat Reduction Agency’s (DTRA’s) most recent Chemical Biological Operational Analysis (CBOA) event in April, Avon Protection was in the unique position of seeing its EXOSKIN boots, gloves and suits put through their paces with the in-service M50/M53 respirator – with extremely positive feedback.
“Exercises such as CBOA are extremely useful, as the reality of a CBRN event is that it is stressful, difficult, long and uncomfortable for the person behind the mask,” Hine said. “So to see that first-hand feedback of how comfortable, lightweight and breathable the garments are, while wearing the rest of their normal gear and conducting extremely strenuous tactical operations, was enormously validating.
“Ultimately we are aiming to keep these operators safe from CBRN threats with our integrated ensemble but knowing that it is enabling them to complete their mission with fewer negative physiological effects at the same time confirms that our approach here is the right one.”
Flexibility of use
It is a strategy that is beginning to bear fruit. In mid-2023, the company’s EXOSKIN boots and gloves were selected by the NATO Support and Procurement Agency (NSPA) to allow NATO nations and partners to place orders under a single contract vehicle. Appealing to such a wide user group, and each nation’s individual doctrine as to the fielding and deployment of CBRN protective system, is, Hine believes, also a challenge solved best with a focus on integration.
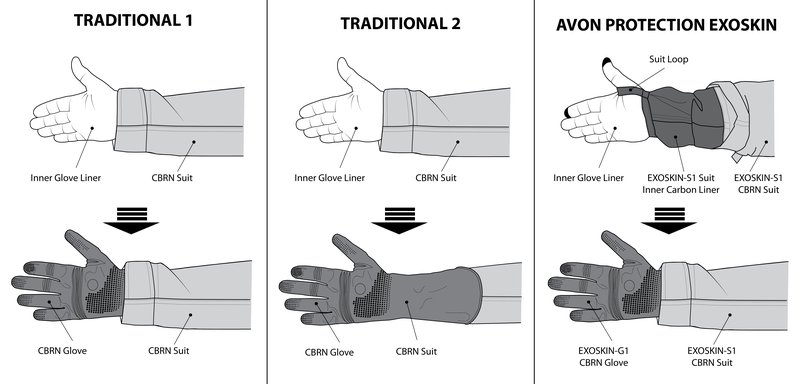
Above: Avon Protection’s EXOSKIN-S1 suit and CBRN glove interface is designed to provide advanced protection against toxic leaks and drips. (Source: Avon Protection)
“Take the interface point between the glove and the suit sleeve,” he said. “Some user groups prefer to wear the glove over the sleeve of the suit, while others do the other way around with the glove under the sleeve. Both options have their advantages, but also have their drawbacks, with the potential for leaks and drips to make their way through a two-layer system.
“In order to maximise the protective integrity of the EXOSKIN-S1 we have developed a unique solution where the inner cotton liner is layered under the glove, then the suit cuff comes down over the top of the glove forming an 'S’ shape in the layers so that there is a much more significant barrier against toxic leaks and drips.”
Ultimately the EXOSKIN-S1 has been designed to offer maximum flexibility of use while it is being worn, but also to meet the different doffing requirements of the user group. Such preferences are most often led by the mission profile and decontamination process of the user. When contaminated, some users will cut the garments off and dispose of them, while others will need to remove the garments carefully in order to clean and reuse; and the results of the design methodology to allow maximum flexibility are evident throughout the EXOSKIN boots, gloves and suit range and their design as a whole system ensemble. Gloves can be worn with or without liner, boots can be worn over or under suit leg cuff, and suit tops are available with full and quarter-length front zip.
“The question goes beyond how to prevent toxins getting through the point at where glove, boot or mask meets suit, but how also to keep the person inside safe while they are getting it off when surface contamination has occurred,” Hine said. “And like everything else, delivering the flexibility to suit all takers is something that can only be managed when a single manufacturer oversees the design and integration of the whole ensemble.”
More from Industry Spotlights
-
The power of partnership: GDMS–UK deepens cooperation with the British Army
In Conversation: Shephard's Gerrard Cowan talks to General Dynamics Mission Systems–United Kingdom’s Chris Burrows about how the company's UK TacCIS business is reshaping battlefield communications through sustained customer engagement, accelerated innovation and ecosystem collaboration.
-
Expanded focus – unleashing the potential of commercial SATCOM for defence
In conversation... Intelsat's Ray Lindenmayer talks to Shephard's Gerrard Cowan about the new capabilities advanced commercial SATCOM technologies can provide for military customers, and how industry and government can best work together to achieve maximum effect in orbit.
-
Enhancing education: How CAE is embracing new technology to boost military training
In Conversation... Shephard's Gerrard Cowan talks to CAE's Marc-Olivier Sabourin about how the training and simulation industry can help militaries achieve essential levels of readiness by leveraging new technology, innovative procurement methods and a truly collaborative approach.
-
Why tactical UAVs are winning on the future battlefield (Podcast)
In Conversation: In this special edition of the Shephard Defence Podcast, Tony Skinner sits down with Dan Slasky, President and CEO of Aeronautics, to explore how cutting-edge tactical unmanned aerial systems are reshaping today’s battlefields.
-
Fincantieri’s Vulcano Class: a new era of versatility and innovation in naval operations
Logistic support ships (LSS) are essential for sustained naval operations, especially during extended deployments far from home ports.
-
Need more flexibility in battle management system delivery?
Systematic’s newest solution, SitaWare BattleCloud, brings greater flexibility to combat information systems and C4ISR.