Power conversion: the value of customisation (free whitepaper)
This industry whitepaper is brought to you by Enercon Technologies Ltd.
Are the benefits of a power conversion solution which truly fulfills the application requirements found in a tailored solution? This white paper reviews the challenges with standardization and offers case-studies detailing how custom solutions were implemented to achieve system qualification.
Introduction
Program managers & acquisition professionals supporting national defence efforts have long sought to drive down cost and schedule risks. One of the simplest ways to achieve this goal is by using components and subsystems conforming to well-established industry standards. The trend of increased standardization holds true in the power conversion market with the growing adoption of both physical and electrical industry standards, such as ATX, VME64x, VITA 62 & VITA 46, and MIL-STD-1275, among others. However, there is a fly in that ointment: the benefits of well-defined design standards come at the cost of a reduced capability to tailor & customize power supply solutions to meet the unique performance requirements prevalent in military systems.
The purpose of this white paper is to explain the important benefits of tailoring power supply design features, specifically considering the latest VMEBus International Trade Association’s (VITA) VPX standards. We’ll consider specific design challenges with standardized power supplies and look into case-studies, in which tailoring was a critical stepping stone towards integration and system qualification.
Customization – A Risk Mitigator
Rugged power supplies capable of addressing unique industry challenges have become a critical design element in today’s military electronics. Mature standards such as MIL-STD-704 and MIL-STD-1275, defining electrical power characteristics, or MIL-STD-461 characterizing electro-magnetic compatibility (EMC) characteristics, have standardized best design practices for engineers. Meanwhile, budget constraints have forced program managers to seek modular, open architecture solutions, to address onerous challenges on behalf of our warfighters.
As such, the VPX form factor has quickly become a design tool engineers leverage to address many of the above standardization challenges, all while improving performance. The standardization of mechanical and electrical features has resulted in VPX products viewed as a “commodity”. However, the benefits of standardization may continue to be outweighed by the challenging performance requirements engineers face.
Output voltages, load current limit levels, stable responses to significant load step, EMC, inrush current surge limitation, and telemetry communication are some of the critical elements of a power supply integrated to a military system. Possessing the ability to customize these, and many other features of a power supply, even within a standardized mechanical form factor, remains an important capability to the design engineering, systems engineering, and testing community.
Figure 1. MILVPX M30600-A 3U Military VPX DC/DC Converter by Enercon Technologies Ltd.
To many, customization is a scary word, suggesting increased cost, schedule slips, or increased technical risk. In reality, customization can actually reduce cost and schedule! A power supply manufacturer who can support tailoring of key features may be a designer’s ally, especially when designing from an existing, field proven baseline product, often with little or no non-recurring engineering (NRE) costs
An excellent example is Enercon Technologies Ltd’s M4065 VPX power supply: a 3U, six output, 600W DC/DC converter with embedded EMI filter; one of many products in the MILVPX product family. The baseline M4065 product complies with the VITA 46 mechanical and VITA 62 electrical specifications, as well as MIL-STD-461 (EMC), MIL-STD-704 (aircraft electric power), MIL-STD-1275 (military vehicle electric power) and MIL-STD-810 (environmental conditions); a set of standards establishing the minimum criteria for any power supply implemented in a defense application.
However, as evident in the following case study, the baseline configuration was not capable of addressing 100% of our customer’s specifications. A recent customer wanted to make use of this off-the-shelf product with its baseline capabilities, but the design required the tailoring of numerous output voltage and current levels to address the requirements of their rugged single board computer (SBC) and storage cards within the enclosure. Starting with the M4065 VPX power supply as a baseline, the Enercon Technologies Ltd engineering team was able to rapidly implement the necessary changes to support the integration of those peripherals, providing a customized power supply that continued to comply with the vast majority of the industry standards.
Adjusting the VS2, VS3, and 3.3V AUX outputs to meet the customer’s unique current and voltage requirements was a low cost, low risk, and rapid solution to enable system level performance. The customer successfully achieved qualification of the system upon first attempt. While the off-the-shelf M4065 was 90% of the solution, Enercon Technologies Ltd’s ability to rapidly tailor the product to the needs of this customer ultimately addressed the unique needs of the warfighter.
Customization does not need to be considered “risky” or expensive and, in sticking with the VITA VPX standards to ensure an open architecture at the system level, can significantly drive lifecycle costs and development time down for the end user Component vs. System Requirements.
— Enercon Technologies Ltd.
To further this point, Enercon Technologies Ltd’s ability to provide increased voltage and current limits at these three outputs, deviating from the VITA standard, ensured a second power supply was not required within the enclosure. This not only saved the cost of a second power supply, but also saved an open card slot to support integration of future product enhancements and capabilities.
This is an excellent case study of how customization does not need to be considered “risky” or expensive and, in sticking with the VITA VPX standards to ensure an open architecture at the system level, can significantly drive lifecycle costs and development time down for the end user Component vs. System Requirements.
Standardization is an industry trend providing positive results for both the cost and schedule of defense programs, large and small. A fine balance between component level specifications and system level specifications is a key aspect in any engineering effort. An excellent example of a component level specification is the VITA 62 VPX standard defining electrical connector parameters, including voltage and current levels. Standards, such as MIL-STD-1275, may be applied at either a component level or system level, to control 28VDC electrical power in a military ground platform.
It can be stated that industry appreciates and values standards, at both the component and system level. However, it is often necessary to deviate from the standard to meet 100% of both component and system level requirements. Every system on the battlefield poses a unique set of challenges, forcing design engineers to make difficult decisions impacting cost, schedule, and risk.
A recent case study involved a customer’s requirement to incorporate a redundant AC power connector into a 3U VPX power supply. This example took customization of a baseline VPX power supply one step further than our previous case study; tailored mechanical and thermal design features.
ABOVE: Figure 2. MILVPX Custom 3U VPX Solution
In this example, a customization effort similarly reduced risk while incorporating important capabilities at a system level. The project started from the mature baseline M4065 3U VPX board layout. A modified mechanical housing was quickly designed around the board to address the redundant input power requirements (a second connector compliant to MIL-DTL-38999) at the system level.
Starting from a 3U VPX form factor, while customizing the mechanical features of the housing, improved thermal management and ensured the integration of other COTS VPX peripheral cards. Within 60 days, a design review provided the customer with enough confidence and data on the modified VPX power supply to begin design modifications to the enclosure and backplane to accommodate the added connector.
Starting from an existing and mature MILVPX product that addressed a large percentage of the power supply performance specification was a no-nonsense and schedule-driven decision that enabled our customer to address requirements. Considering our earlier example, a VPX-form factor single board computer required 360W of power, exceeding the VITA 62 standard for the VS2 connector contact.
While deviating from the VITA electrical standard, the desired 3U mechanical form factor was not changed, ensuring an open architecture system and retention of the benefits of the VPX form factor. At a system level, a standardized chassis and backplane could be maintained, along with use of peripheral devices, reducing total lifecycle costs and maximizing the intended nature of standardized enclosure designs. Supporting both component and system level requirements is achievable by tailoring the design of standard products.
Electro-Magnetic Compatibility (EMC) & Standardization
In the ever-evolving world of defense electronics; higher power densities, increasing current and faster switching, and electro-magnetic compatibility (EMC) continues to be one of the most challenging endeavors of the system designer. Modern power switches offer significantly higher switching speeds. This means that the rise and fall times for both voltage and current waveforms are much shorter - a root cause of many electro-magnetic interference (EMI) issues in switching power supply design.
As such, solutions to address the litany of EMI challenges need to remain agile and creative when it comes to power supply design. Standardization on the other hand, encourages repeatability and de-incentivizes change. To solve EMI issues, customization is a key element in the toolbox of the design engineer.
To qualify a power supply, it is tested in cascade with a line impedance stabilization network (LISN) to standardize test results and simulate the run of cables feeding the tested item. Typically, power supplies installed in small platforms are allowed to be tested with low inductance LISN, so they will not become unstable and oscillate.
However, in scenarios where long cable runs are prevalent the standard 50 μH must be used. A recent customer approached Enercon Technologies Ltd interested in a 3U, 350W converter for integration in an airborne application. The customer stated that the converter must be tested for compliance with MIL-STD-461F when connected to the power line through 50 μH LISNs. The Enercon Technologies Ltd R&D team modified our existing off-the-shelf M4065 product, integrating a larger bulk capacitance to help support the 50μH inductance requirement. Again, deviating from the VITA 62 electrical standard to rapidly address a unique EMC requirement provided the customer a schedule-friendly, low risk solution.
Powering Non-Standard Loads with Standard Power Supplies
The standard VPX chassis is commonly used by integrators as an enclosure for a wide variety of applications, including radar, electronic warfare, communications, and more. Each application brings its own unique set of performance and operational requirements. In one recent example, a customer requested a VPX power supply to feed a radar load, made up of digital circuits (signal conditioner), analog low power circuits (pre-amplifier) and analog high-power circuits (power amplifier). The form factor and connector were standard VITA 62 & 46, but the output voltages and current limits were completely different, with odd voltage levels, such as 6VDC for the GPS board, 5.5VDC for the wideband amplifier and 28VDC for the power amplifier. Not only were the voltage values not standardized, the digital and analog outputs' return paths were required to be isolated from one another.
Customization by the Enercon Technologies Ltd engineering team began from the off-the-shelf M4065 DC/DC converter baseline product. The design team tailored the output voltages according to the requirement and separated the outputs into two isolated groups. This design approach helped the customer achieve a complete radar design with an integrated power solution in a single VPX chassis, all of which occurred in a short schedule of only three months from PO to delivery!
The ability to deviate from design standards can be a priceless aid for engineers in order to meet the unique performance requirements prevalent in military platforms
— Enercon Technologies Ltd.
Conclusion
The benefits of defined design standards are numerous, especially in support of open architecture system designs reducing lifecycle costs and development time. However, the ability to deviate from design standards can be a priceless aid for engineers in order to meet the unique performance requirements prevalent in military platforms.
We’ve presented a number of case studies and examples where customization of power supplies provided a discrete and obvious advantage to the design engineer to meet performance specifications. Whether it be saving a card slot in a chassis, reducing the number of power supplies required or addressing a unique EMC requirement, customization reduced total system cost and technical risk to put increased capabilities rapidly into the hands of national defence organizations. Customization is available within the defense power supply market, engineers should heed industry trends to improve standardization, but understand customization can be a cost effective and low-risk approach to address requirements.
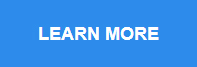
More from German Defence Industry Special Report
-
German Army to upgrade combat vehicle sims
Saab is to carry out a mid-life upgrade programme of the German Army’s AGDUS combat vehicle simulators, the company announced on 4 December. The $18.9 …
-
Saab to operate German Army’s GÜZ
Saab will operate the German Army’s Combat Training Centre, Gefechtsübungszentrum Heer (GÜZ) between 2020 and 2026 under a new contract announced on 2 December. The …
-
Rheinmetall showcases indirect fire capabilities
Rheinmetall has taken part in a demonstration in South Africa to showcase its indirect fire capabilities, the company announced on 27 November. The test fire …
-
Unique requirements of uninterruptible power supplies for naval applications (free whitepaper)
A true Naval qualified – MIL-STD-1399 and MIL-DTL-901 - Uninterruptible Power Supply (UPS) must meet stringent requirements, consistent with a military quality solution. This white …
-
Important factors in vehicle power distribution (free whitepaper)
The purpose of this article is to define the importance of flexibility and customisation in the type of PDU selected for military vehicle and aircraft …
-
Germany's latest industry developments (video)
Watch a summary of the latest developments in the German Defence Industry. Land On land KMW has begun deliveries to Denmark and Germany of the …